Understanding Optical Parts Processing: Hot, Cold, and Special Techniques
Understanding Optical Parts Processing: Hot, Cold, and Special Techniques
7/26/20244 min read
Hot Processing: The Foundation of Optical Parts
Hot processing serves as the crucial initial step in the manufacturing of optical parts, primarily focusing on the preparation and formation of optical parts blanks. This phase involves a series of controlled heating processes, where raw materials are subjected to high temperatures to achieve the desired shape and size. The materials commonly used in hot processing include various types of glass and crystal, each chosen based on the specific optical properties required for the final product.
One of the key components in hot processing is the furnace, which is designed to reach and maintain the high temperatures necessary for melting and shaping the materials. Different types of furnaces are employed depending on the material and the complexity of the optical parts being produced. Continuous furnaces, for instance, are used for large-scale production, while batch furnaces are suitable for smaller, more specialized runs.
Molds are another essential element in hot processing. These molds, often made from durable materials such as graphite or refractory metals, are used to shape the molten material into blanks. The precision of these molds is critical, as any imperfections can affect the quality of the final optical parts. Temperature control is maintained rigorously throughout the process to ensure uniformity and to prevent defects such as bubbles or inclusions within the material.
Achieving the correct blank shape and size is a fundamental objective of hot processing. This sets the stage for subsequent cold and special processing techniques, where the optical parts are further refined and polished to meet exact specifications. The accuracy and quality of the blanks produced during hot processing significantly impact the efficiency and success of later stages in the manufacturing process.
In summary, hot processing lays the groundwork for the entire optical parts manufacturing process. By meticulously controlling temperature, utilizing precise molds, and selecting appropriate materials, manufacturers can produce high-quality optical blanks that serve as the foundation for further processing and ultimately, the creation of superior optical components.
Cold Processing: Precision and Refinement
Cold processing is an essential phase in the production of high-quality optical parts. It encompasses a series of meticulous steps aimed at refining the optical components to meet precise specifications. This process begins with bulk abrasive or solid abrasive sawing, where large pieces of optical material are cut into smaller, more manageable sections using abrasive blades. This initial step is crucial for shaping the raw material into a form that is closer to the desired dimensions.
Following sawing, rough grinding is employed to further shape and size the optical parts. This step involves the use of coarse abrasives to remove substantial amounts of material, quickly bringing the parts closer to their intended form. The focus during rough grinding is on efficiency and material removal, rather than achieving a smooth finish.
Once rough grinding is complete, fine grinding takes over. This process utilizes finer abrasives to achieve a more precise shape and smoother surface finish. Fine grinding is critical for bringing the optical parts to their near-final form, ensuring they meet stringent dimensional and surface quality requirements.
Polishing is the next step, where the optical parts are given a high degree of smoothness and clarity. This is achieved through the use of ultra-fine abrasives and polishing compounds, which remove the last traces of surface irregularities and impart a mirror-like finish. The precision of this step cannot be overstated, as the quality of the final optical part largely depends on the effectiveness of the polishing process.
Centring edge grinding is the final step in the cold processing phase. This involves grinding the edges of the optical parts to ensure they are perfectly centered and aligned. This step is crucial for ensuring that the optical parts perform correctly in their intended applications. Specialized equipment is used to achieve the necessary precision, highlighting the importance of technology and expertise in this phase of optical parts processing.
Each step in the cold processing phase plays a vital role in refining optical parts to their final specifications. The use of specialized equipment and the emphasis on precision at every stage underscore the complexity and importance of this phase in the overall production process.
Special Processing: Enhancing Surface Performance
In the realm of optical parts processing, special techniques are employed to enhance the performance characteristics of the polished surfaces without altering their shape or size. These specialized methods are crucial in ensuring that optical parts meet the stringent requirements of various applications. Among the most significant of these techniques are coating, scaling, photographing, and gluing. Each method plays a vital role in the final quality and functionality of the optical components.
Coating processes are paramount in improving the efficiency and durability of optical parts. Various types of coatings, such as anti-reflective and protective layers, are applied to the surface of optical elements to minimize reflection losses and protect against environmental factors. Anti-reflective coatings, for instance, enhance the transmission of light through the optical part, thereby increasing its efficiency. Protective coatings, on the other hand, provide a barrier against scratches, moisture, and other potential damages, extending the longevity of the optical elements.
Scaling, although less commonly discussed, is another critical processing technique. It involves the precise measurement and adjustment of the optical surface to ensure that it meets the exact specifications required for its intended use. This process guarantees that the optical parts function optimally within their designated systems.
Photographing, or surface inspection, is a quality control measure that ensures the surface integrity of the optical parts. This process involves using high-resolution imaging techniques to detect any imperfections or irregularities on the surface. By identifying and addressing these issues early on, manufacturers can prevent defects from affecting the performance of the final product.
Gluing is essential for the assembly of multi-component optical systems. This technique involves bonding optical elements together using adhesives that are specifically designed to maintain the optical clarity and alignment of the parts. Proper gluing ensures that the assembled optical system functions as a cohesive unit, delivering the desired performance without compromising the individual characteristics of each component.
Through these special processing techniques, the durability, efficiency, and overall performance of optical parts are significantly enhanced, ensuring that they meet the high standards required for their diverse applications.
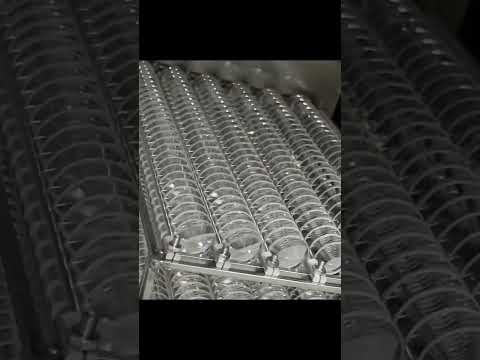