Understanding Optical Mirror Coatings: From Aluminum to Gold and Silver
Optical Mirror coatings are essential components in optical applications that enhance reflectivity and improve the performance of various optical devices. These coatings are primarily used to create reflective surfaces in instruments such as telescopes, microscopes, lasers, and others.
9/23/20244 min read
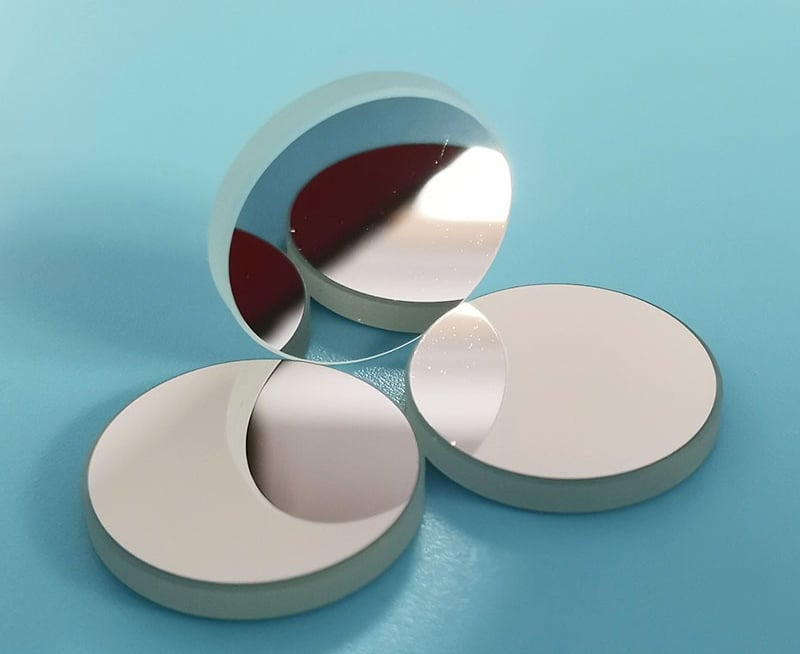

Introduction to Mirror Coatings
Mirror coatings are essential components in optical applications that enhance reflectivity and improve the performance of various optical devices. These coatings are primarily used to create reflective surfaces in instruments such as telescopes, microscopes, lasers, and other optical systems. The fundamental role of mirror coatings lies in their ability to reflect light efficiently, thereby ensuring that the maximum amount of light reaches the observer or sensor, which is critical in generating clear and accurate images.
Different materials are employed for mirror coatings, each possessing distinct optical properties that cater to specific spectral ranges. Aluminum is one of the most commonly used materials due to its cost-effectiveness and good reflectivity across a wide range of wavelengths. When coated with aluminum, surfaces can achieve reflectivity values exceeding 90% in the ultraviolet, visible, and near-infrared spectra. However, aluminum does have limitations, particularly in the infrared region, where its performance may not be optimal.
Silver and gold are two additional materials frequently utilized in mirror coatings, each offering unique advantages. Silver, for instance, boasts the highest reflectivity in the visible spectrum, often more than 95%, making it an excellent choice for applications requiring maximum brightness and image clarity. However, silver is susceptible to tarnishing, which necessitates protective layers. Gold, on the other hand, excels in the infrared region, making it suitable for applications like thermal imaging where reflectivity in those wavelengths is paramount. While gold coatings may come at a higher cost, their longevity and stability under various environmental conditions often justify the investment.
In conclusion, selecting the appropriate mirror coating material is crucial for optimizing the performance of optical devices. By understanding the properties of these materials, designers and engineers can make informed decisions that enhance the effectiveness of their optical systems.
Protected Aluminum Coating
Protected aluminum coating has emerged as the most widely utilized mirror coating for applications in the visible and near-infrared spectrum. This coating consists of a thin layer of aluminum that is subsequently protected by a layer of dielectric material, typically silica or other optical coatings. The primary purpose of this protective layer is to enhance the durability of the aluminum while maintaining its reflective properties. The combination of aluminum and its protective layer results in a mirror that offers superior performance in various applications.
One of the defining advantages of protected aluminum coatings is their high reflectance across a broad range of wavelengths. In the visible spectrum, the reflectivity can exceed 90%, making it an excellent choice for optical components, such as mirrors and beam splitters. Furthermore, the near-infrared reflectance remains comparably high, which is a crucial feature for industries that rely on infrared technology, such as telecommunications and thermal imaging.
In terms of applications, protected aluminum coatings excel in fields such as astronomy and microscopy, where precise light manipulation is critical. Its robust nature allows it to withstand harsh environmental conditions, making it ideal for outdoor telescopes and other instruments subjected to variable temperatures and atmospheric effects. Additionally, the coating is commonly used in lighting applications, where high efficiency and longevity are essential.
When comparing protected aluminum to other coatings, such as protected silver or gold, it can be noted that while silver coatings boast higher initial reflectance, they are more susceptible to tarnishing and environmental degradation. Conversely, gold coatings provide excellent reflectance in the infrared range but are typically more expensive. Therefore, protected aluminum serves as a balanced option, combining affordability, durability, and high reflectance, solidifying its status in various optical applications.
Enhanced Aluminum and UV Enhanced Aluminum Coatings
Enhanced aluminum coatings are specifically designed to improve the reflective properties of standard aluminum, making them an optimal choice for specific wavelength ranges. These coatings exhibit notable effectiveness in the 400nm to 650nm spectrum, which corresponds with a significant portion of visible light. In applications such as lighting, lasers, and photographic equipment, enhanced aluminum coatings are often preferred due to their ability to maximize light transmission and minimize losses. Their utility is evident in various optical setups, where increased reflectivity translates to improved performance, providing brighter and more vivid outputs in optical systems.
On the other hand, UV enhanced aluminum coatings are formulated to excel in the ultraviolet range, particularly from 250nm to 400nm. This makes them invaluable in applications that require high efficiency in wavelengths not reached by standard coatings. Such coatings are crucial for specialized equipment, including photomultiplier tubes, ultraviolet lasers, and specific analytical instruments used in scientific research. The significance of UV enhanced aluminum lies in its robustness against the potentially damaging effects of UV exposure, enabling reliable performance in environments where conventional aluminum might fail.
When choosing between enhanced aluminum and UV enhanced aluminum coatings, it is essential to consider the specific requirements of the optical application at hand. For instance, applications focused on visible light will greatly benefit from enhanced aluminum options, whereas those needing UV performance will find UV enhanced aluminum indispensable. Understanding these unique reflective properties and their implications in different scenarios ultimately helps in selecting the appropriate coating for any given optical system.
Protected Gold and Protected Silver Coatings
Protected gold and protected silver coatings play a pivotal role in various optical applications, particularly due to their unique reflective properties. Protected gold coatings are primarily utilized in infrared (IR) applications, where they exhibit superior performance. The effectiveness of these coatings in the near-infrared spectrum is attributed to their high reflectivity and minimal absorption, which is essential for infrared imaging and sensing technologies. The addition of a protective layer not only enhances durability but also maintains the excellent reflective qualities inherent in gold. This makes protected gold an optimal choice for applications such as thermal imaging and spectroscopy where minimal signal loss is crucial.
On the other hand, protected silver coatings are recognized for their exceptional broad-spectrum reflectivity, encompassing both visible and infrared ranges. Silver inherently possesses the highest reflectivity among metals across a broad spectrum, making it ideal for various optical systems that require effective light management. The protective layer, often made from dielectric materials, safeguards the silver coating against oxidation and degradation, thus prolonging its lifespan and maintaining performance reliability. These coatings are widely used in applications ranging from mirrors in telescopes to reflective surfaces in lighting and display technologies.
The versatility of protected gold and silver coatings enables their application in multiple domains. For instance, protected gold coatings are integral to advanced IR systems such as thermal cameras and detectors, while protected silver coatings are commonly found in laser systems and high-performance optics. Both types of coatings contribute significantly to the efficiency and effectiveness of optical systems, enhancing their capability to manage light across varying wavelengths.
Understanding the properties and applications of protected gold and protected silver coatings underscores their importance in modern optical design and engineering, ultimately optimizing system performance.